Sink Mark Depth Calculation
Designing plastic moldings light and strong
often requires the use of strengthening ribs, the rib depth
generally determines strength and stiffness of the structure. Where a molding provides asthetic and load bearing qualities,
strength and surface finish are often incompatable. This is where Moldflow simulation technology can
help optimise the design.
Sink
mark visibility can be very subjective, and is often dependant on
many factors such as lighting, surface texture and less tangible
factors such as experience / expectation of the observer. Past
research suggests that on textured surfaces sink mark depths of
0.040mm are generally not visible to the trained eye while sink
marks deeper than 0.075 mm are evident even to the untrained eye.
On high gloss surfaces sink marks less than 0.015 mm can be quite
visible depending on light conditions.
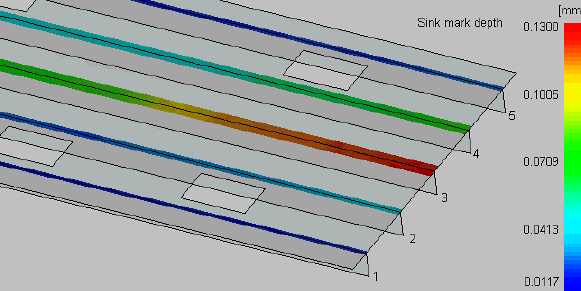
The image
above displays sink mark depth prediction based on a flat plate
with wall thickness of 2.5 mm, on the "B surface" ribs with
thickness variation from 0.8 mm to 2.5 mm as
follows:-
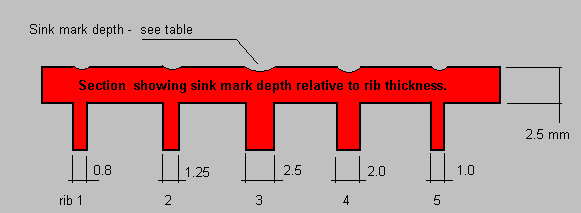
Table showing sink mark depth in "mm"
Vs flow distance @ 70 Mpa hold - PP .
|
|
|
|
|
|
Sink 100 mm from the gate. |
|
|
|
|
|
Sink 175 mm from the gate. |
|
|
|
|
|
Sink 200 mm from the gate. |
|
|
|
|
|
Pink shading
indicates visible sink on a textured finish.
Factors effecting
sink mark depth :
Rib / wall thickness
ratio. |
|
Hold time. |
Fillet radii. |
|
Melt temperature . |
Distance from gate. |
|
Tool temperature. |
Straight
ribs or cross ribs |
|
Cooling time.. |
Hold pressure. |
|
Material Crystaline / Amorphous
. |
For more information or a quotation please see our contact and RFQ pages.
|