Search For Polymer Materials
Materials Processing Guide
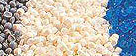
|
Access generic polymer materials processing guide.
Click the link to the right for big screen viewing or bookmark. www.moldtrial.mobi in your mobile phone browser. |
Materials
Guide
|

|
- Heat Distortion
Temperature
|
|
- Maximum service temperature
|
|
|
|
|
|
|
- Melting Point Temperature
|
|
Material Applications
Generic grades
|
Typical Applications
|
ABS
|
Automotive (instrument and interior trim panels, glove compartment doors, wheel covers, mirror housings, etc.), refrigerators, small appliance housings and power tools applications (hair dryers, blenders, food processors, lawn mowers, etc.), telephone housings, typewriter housings, typewriter keys, and recreational vehicles such as golf carts and jet skis.
|
PA6
|
Used in many structural applications because of its good mechanical strength and rigidity. It is used in bearings because of its good wear resistance.
|
PA12
|
Gear wheels for water meters and business machines, cable ties, cams, slides, and bearings.
|
PA66
|
Competes with PA 6 for most applications. PA 66 is heavily used in the automotive industry, appliance housings, and generally where impact resistance and strength are required.
|
PBT
|
Household appliances (food processor blades, vacuum cleaner parts, fans, hair dryer housings, coffee makers, etc.), electronics (switches, motor housings, fuse cases, key caps for computer keyboards, connectors, fiber optic buffer tubing, etc.), automotive (grilles, body panels, wheel covers, and components for doors and windows, etc.)
|
PC
|
Electronic and business equipment (computer parts, connectors, etc.), appliances (food processors, refrigerator drawers, etc.), transportation (headlights, taillights, instrument panels, etc.).
|
PC+ABS
|
Computer and business machine housings, electrical applications, cellular phones, lawn and garden equipment, automotive components (instrument panels, interior trim, and wheel covers).
|
PC+PBT
|
Gear cases, automotive (bumpers); applications which require chemical and corrosion resistance, high heat resistance, high impact strength over wide temperature ranges, and high dimensional stability.
|
HDPE
|
Containers in refrigeration units, storage vessels, household goods (kitchenware), seal caps, bases for PET bottles, etc. Major use is in blow-molding applications (packaging applications)
|
LDPE
|
Closures, bowls, bins, pipe couplings.
|
PEI
|
Automotive (engine components: temperature sensors, fuel and air handling devices), electrical/electronics (connector materials, printed circuit boards, circuit chip carriers, explosion proof boxes), packaging applications, aircraft (interior materials), medical (surgical staplers, tool housings, non implant devices).
|
PET
|
Automotive (structural components such as mirror backs, and grille supports, electrical parts such as head lamp reflectors and alternator housings), electrical applications (motor housings, electrical connectors, relays, and switches, microwave oven interiors, etc.), industrial applications (furniture chair arms, pump housings, hand tools, etc.).
|
PETG
|
PETGs offer a desirable combination of properties such as clarity, toughness, and stiffness. Applications include medical devices (test tubes and bottles), toys, displays, lighting fixtures, face shields, and refrigerator crisper pans.
|
PMMA
|
Automotive (signal light devices, instrument panels, etc.), medical (blood cuvettes, etc.), industrial (video discs, lighting diffusers, display shelving, etc.), consumer (drinking tumblers, stationery accessories, etc.).
|
POM
|
Acetals have a low coefficient of friction and good dimensional stability. This makes it ideal for use in gears and bearings. Due to its high temperature resistance, it is used in plumbing (valve and pump housings), and lawn equipment.
|
PP
|
Automotive (mostly mineral-filled PP is used: dashboard components, ductwork, fans, and some under-hood components), appliances (door liners for dishwashers, ductwork for dryers, wash racks and lids for clothes washers, refrigerator liners, etc.), consumer products (lawn/garden furniture, components of lawn mowers, sprinklers, etc.).
|
PPE
|
Household appliances (dishwasher, washing machine, etc.), electrical applications such as control housings, fiber-optic connectors, etc.
|
PS
|
Packaging, housewares (tableware, trays, etc.), electrical (transparent housings, light diffusers, insulating film)
|
PVC
|
Water distribution piping, home plumbing, house siding, business machine housings, electronics packaging, medical apparatus, packaging for foodstuffs, etc.
|
SAN
|
Electrical (receptacles, mixer bowls, housings, etc. for kitchen appliances, refrigerator fittings, chassis for television sets, cassette boxes, etc.), automotive (head lamp bodies, reflectors, glove compartments, instrument panel covers, etc.), household appliances (tableware, cutlery, beakers, etc.), cosmetic packs, etc.
|
This topic describes some important material characteristics to consider before selecting a thermoplastic material grade. The material that you select will depend on the characteristics that you require.
The crystallinity of a material identifies the state of the polymer at processing temperatures, and can range from amorphous to crystalline states. Amorphous polymers are devoid of any stratification, and retain this state at ambient conditions. Crystalline polymers have an ordered arrangement of plastic molecules, allowing the molecules to fit closer together. Therefore, they are more dense than amorphous polymers. The rate of crystallinity is a function of temperature and time. Rapid cooling rates are associated with lower levels of crystalline content and vice versa. In injected molded parts, thick regions cool slowly relative to thinner regions, and therefore have a higher crystalline content and volumetric contraction.
The mold temperature is the temperature of the mold where the plastic touches the mold. Mold temperature affects the cooling rate of the plastic, and cannot be higher than the ejection temperature for a particular material. The temperature of the molten plastic is the melt temperature. Increasing the melt temperature reduces the viscosity of a material, which also reduces shear stress. This results in less material orientation during flow. Additionally, the material is hotter which decreases the frozen layer thickness. Decreasing the frozen layer means that shear is less since the constriction to flow is less.
The
specific heat (Cp) of a material is the amount of heat required to raise the temperature of a unit mass of material by one degree Centigrade. It is essentially a measure of a material's ability to convert heat input to an actual temperature increase. It is measured at zero pressure and a range of temperatures, or averaged across the temperature range of 50°C to the material's maximum processing temperature.
The
Thermal Properties
tab of the
Thermoplastic material
dialog shows the specific heat data in tabular format, as follows.
- Each row of the table shows the specific heat data at a given temperature. In many cases, the table consists of one row.
- T
is the test temperature. The unit of measure is C, Celsius.
- Cp
is the specific heat at the given temperature. The unit of measure is J/kg-C, Joules per kilogram Celsius.
- The Heating/cooling rate is the rate at which the material was heated or cooled when tested. Typically it is cooled, and this is represented by a negative value, usually -0.3333. The unit of measure is C/s, the temperature change in degrees Celsius, per second.
The
thermal conductivity (k)
of a material is the rate of heat transfer by conduction per unit length per degrees Celsius. It is essentially a measure of the rate at which a material can dissipate heat. It is measured under pressure and at a range of temperatures, or averaged across the material's melt temperature range. The unit of measure is W/m-C, Watts per meter Celsius.
The
Thermal Properties
tab of the
Thermoplastic material
dialog shows the thermal conductivity data in tabular format, as follows.
- Each row of the table shows the thermal conductivity data at a given temperature. In many cases, the table consists of one row.
- T
is the test temperature. The unit of measure is C, Celsius.
- k
is the thermal conductivity at the given temperature. The unit of measure is W/m-C, Watts per meter Celsius.
- The Heating/cooling rate is the rate at which the material was heated or cooled when tested. Typically this value is zero. The unit of measure is C/s, the temperature change in degrees Celsius, per second.
The viscosity of a material is a measure of its ability to flow under an applied pressure. Polymer viscosity is dependent on temperature and shear rate. In general, as the temperature and shear rate of the polymer increases, the viscosity will decrease, indicating a greater ability to flow under an applied pressure. The material database provides a viscosity index for materials, in order to compare ease of flow. It assumes a shear rate of 1000 1/s and indicates the viscosity at the temperature specified in brackets.
To account for material compressibility during a flow analysis, Moldflow provides PVT models. A PVT model is a mathematical model using different coefficients for different materials, giving a curve of viscosity against pressure against temperature. An analysis based on PVT data is more accurate but computationally intensive - through iterations for temperature and pressure per node. However, this makes it particularly suited to complex models that have sudden and large changes in thickness.
As plastics cool, there is a significant change in their dimension, due to volumetric shrinkage. The main factors that affect shrinkage are cool orientation, crystallinity, and heat concentrations.
Transparent plastic under stress can exhibit stress birefringence, where the speed of light through the part depends on on the polarization of the light. Birefringence can result in the transmission of unevenly-polarized light and in double images. Some materials are more prone to stress birefringence than others.
Composite materials contain fillers that are added for injection molding. Adding a filler to a polymer can increase the strength of the polymer and ensure that good quality parts are produced. Most commercial composites contain 10-50% fibers by weight, which are regarded as being concentrated suspensions, where both mechanical and hydrodynamic fiber interactions apply. In injection-molded composites, the fiber orientation distributions show a layered nature and are affected by the filling speed, the processing conditions and material behavior.

ABS ABS ABS GPS HIPS SAN ASA SBS PC PMMA PES PSU PUR FPVC RPVC PP PPO HDPE LDPE PA6 PA66 PA11 PA12 PBT PET POM POM PPS
|
Acrylonitrile Butadiene Styrene Plating High Heat Polystyrene High Impact Polystyrene Styrene Acrylonitrile Acrylate Styrene Acrylonitrile Styrene Butadiene Polycarbonate Polymethyl Methacrylate Acrylic Polyethersulfone Polysulfone Polyurethane Flexible Polyvinyl Chloride Rigid polyvinyl Chloride Polypropylene Polyphenylene Oxide High Density Polyethlene Low Density Polyethlene Nylon 6 Nylon 66 Nylon 11 Nylon 12 Polybutylene Terephthalate Polyethylene Terephthalate Polyoxymethylene Homo Polyoxymethylene Copolymer Polyphenylene Sulphide
|
Moldflow
Engineering Services
Moldflow Plastic Adviser, Moldflow Mpi, Mold flow communicator and Mold Adviser are Mould flow software products for simulating the injection molding of plastic materials. Moldflow is the registered trademark Moldflow Corporation & Moldflow Europe ltd as advised in many trade magazine publications and press releases.
Imtech Design are Moldflow Gold Certified Plastic Flow Simulation Consultants and Engineers.
Click for Material data sheets
Materials Process Guide
Translate Page
|
|